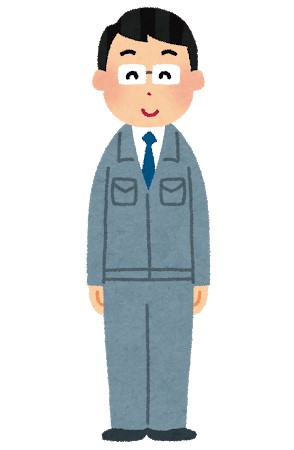
こんにちは、れおねるです。
今回は原料メーカー視点から、その品質を担保するための
プロセス開発の視点について説明します。
プロセス開発とはラボから工業規模への適応
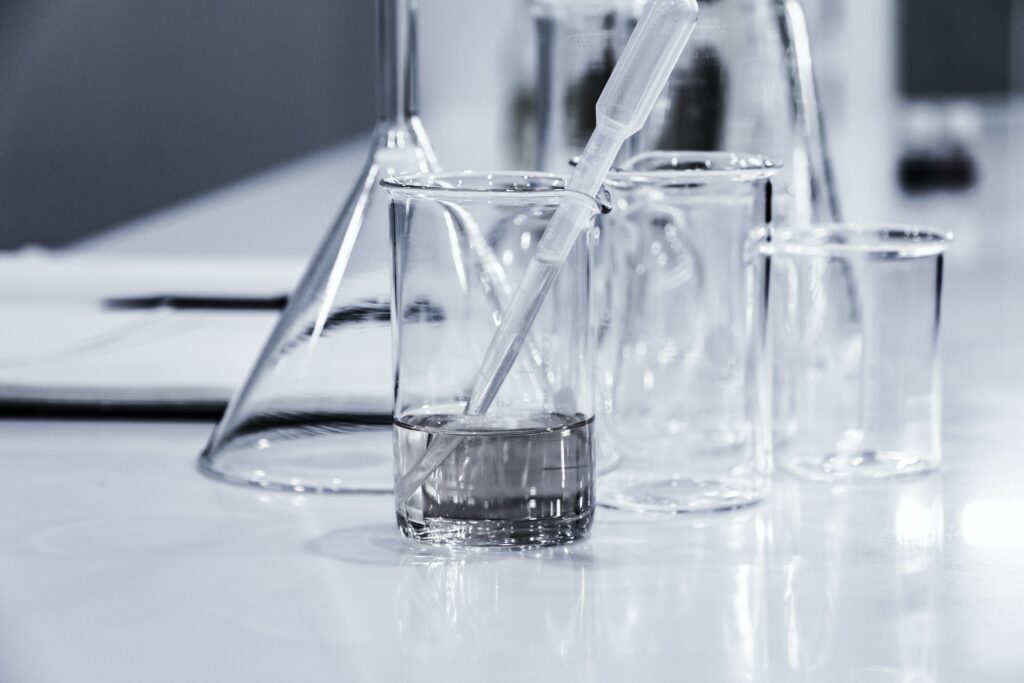
企業によって意味合いが異なったり、生産技術と一緒くたになっている事もありますが、ここでは研究所レベルから工業レベルへの生産工程開発をプロセス開発とします。
ラボで新しい製品や既存品の改良製法が実現できたとき、次に「どうやって工業規模で生産するか」を考える必要があります。
ここでプロセス開発者が持っている化学工学の知見を活かし、実験で試行錯誤しながら理想的な生産工程を確立する事を目指します。
今回は半導体化学品のプロセス開発をするとき、何が大事なのかを説明します。
半導体化学品のプロセス開発の視点
装置や部品の材質選定が何より重要
製品を目的の規格まで上げるためには化学工学の知見が不可欠ですが、分離技術だけで半導体用途のグレードまで上げるのには限界があります。
また、それほど特殊な分離技術を利用しているのではなく、皆さんが学生時代に学んだ単位操作を利用しており、選択肢もそう多くありません。
では、何を重視しているかと言うと…
- 半導体化学品ではそれ以上に目的の製品を製造するための環境を整える事が大事。
- 特に、装置や部品の材質選定が何より重要。
具体的には、半導体化学品は液体の製品が多いのですが、接液している装置自体もしくは装置に使っている部品の材質が製品の溶媒特性に合っている物でなければ、そこから不純物が溶出してしまい、規格不適合品となってしまいます。
明らかに溶媒特性と合っていない材質であれば分かりやすいのですが、規格ppbオーダーの製品を製造する場合は、例え耐久性が公表されている材質であっても、それを鵜呑みせずに材質選定する必要があります。
例えば、テフロンのようなフッ素樹脂は何にでも耐久性のある材質のように思えますが、実はそうではなく、「テフロン選んでおけばOK」と盲信するのは非常に危険です。
テフロンのようなフッ素樹脂材料については、下記の記事をご覧ください。
- 目的に合っていない製造環境が構築される
- 品質低下に繋がり、大袈裟に言えば会社の信用を失う
- 少なくとも原料メーカーの立場では、材質選定が製品の品質を決める生命線
そして、それは実機へ移行するときに材質選定するのではなく、プロセス開発の段階で材質選定を行って実機と同じ環境を整え、そこからスケールアップに必要なプロセスデータを取得していきます。
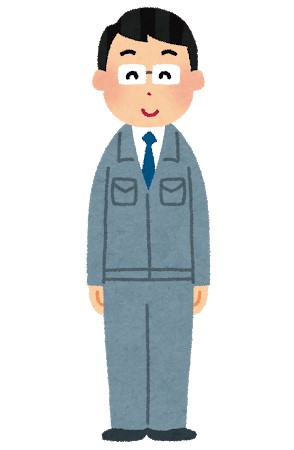
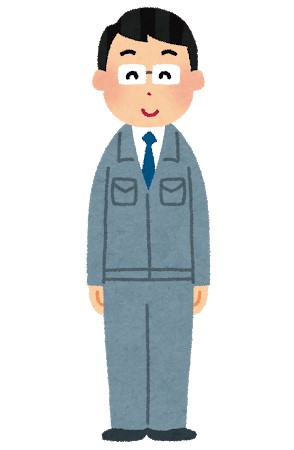
材質選定は最も大事な技術の一つです。
普段何気なく使っている部品も、先人達が品質に合うように、試行錯誤しながら導入したものがあるのではないでしょうか?
プロセスの検討
前項では材質選定について力説しましたが、もちろんプロセス検討も大事な技術です。利用している技術は反応、蒸留、抽出、晶析、乾燥など、至って一般的な単位操作を利用します。
しかし、半導体化学品は1回の製造量が少なく、ほとんどがバッチプロセスとなります。前職は製品ごとに専用プラントがあり、現職は多品種多目的プラントとなっているので、扱っている製品や掲げているビジネス手法によって変えているのではと考えています。
半導体目的のグレードまで品質を上げるためには、一工夫加える必要があります。
例えば…
- 蒸留塔内部の構造選定&還流操作方法の検討
- 晶析での最適な粒度分布検討&撹拌操作
- 反応の終点管理
- 圧力計、測温抵抗体、流量計など計測器の種類・材質選定
- 単位操作を繋ぐ配管、ろ過器等の材質選定
(また材質選定が出てきましたね。) - 装置洗浄技術 etc…
バッチプロセスを利用する場合、反応の終点管理はどこの化学メーカーでもやっていますが、「全く同じ成分表の製品を納めてください」という顧客の要望があったとしたら、主生成物だけでなく、他の副生成物の成分比率も合わせる必要があります。
そのため、どのプロセスデータに着目して反応終点とするか、十分に検討する必要があります。
また、計測器については、品質の観点から実プラントで扱えない種類もあるので、プロセス検討する上で計測器の選定も重要になります。
装置稼働率の検討
前項で、半導体化学はバッチプロセスが多いと書きましたが、プロセス検討が全体ではなく一つの単位操作に限定した場合、その前後のプロセスに影響が出ないか、単位操作の処理時間をガントチャートで作成し、設備毎の稼働率を確認する必要があります。
特に、バッチプロセスでは、装置の遊休時間が多くなることは、生産性の悪いプロセスとなってしまいます。
そのため、各装置の遊休時間を如何に少なくするかを検討する事も、プロセス開発の役目でもあります。
まとめ
今回は、原料メーカー視点ではありますが、品質最重要な半導体化学品がどのような視点でプロセス開発をしているか、以下3点を説明しました。
- 半導体化学品のプロセス開発は、材質選定が肝である
- プロセス検討も細かな所で一工夫必要である
- ガントチャートで設備稼働率を確認する必要がある
社会人で使える化学工学に関するウェブサイトを知りたい方は、下記の記事を参照ください。
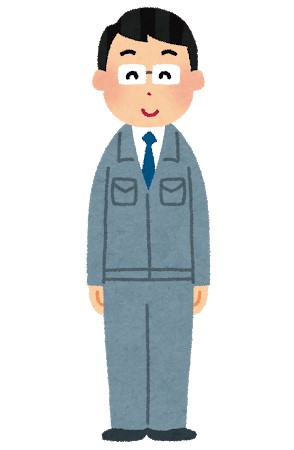
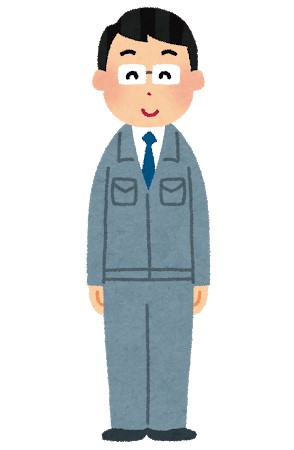
最後までご覧いただき、ありがとうございました!
コメント